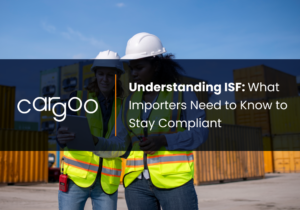
Understanding ISF: What Importers Need to Know to Stay Compliant
Simplify ISF compliance for U.S. ocean imports. Learn how Cargoo helps you stay compliant and avoid costly delays.
Demurrage and detention fees are familiar, visible, and frustrating for many supply chain managers. The problem isn’t that these charges are unknown—they’re there, in the contract, for everyone to see. But by the time charges surface, it’s usually too late to do anything about them. You end up chasing explanations, arguing over who’s responsible, and dealing with issues long after they’ve occurred. Meanwhile, your supply chain continues to move forward, throwing new challenges your way.
The reality is that demurrage and detention costs often get ahead of you, not because they’re impossible to manage, but because common problems in logistics make them hard to control. Let’s break down why this happens and where things go wrong.
Supply chain visibility is a team effort, and when one party drops the ball, the whole process suffers. Communication between carriers, freight forwarders, and cargo owners is often disjointed. This lack of coordination can result in containers not being picked up or returned on time, leading to unnecessary demurrage and detention costs.
Demurrage and detention charges are not fully avoidable, but they can be managed more effectively with the right approach. Here’s how supply chain managers can better prepare and reduce the risk of unexpected fees:
Understanding your contracts is critical. You need a system that ties your contract terms directly to the shipments booked under those contracts. This gives you contextual visibility—the ability to see relevant contract details when and where you need them. With this visibility, you can better track free time, avoid surprises, and take timely action when shipments are nearing their contract limits.
If you’re investing in demurrage and detention software, make sure it offers exception management. This functionality can give you a heads up when charges are accumulating, or when your shipment is at risk of incurring demurrage or detention fees. While you won’t be able to avoid additional charges entirely, a good exception management system ensures you’re not blindsided by charges after the fact. The earlier you know, the more time you have to act.
Coordination is key. Make sure you understand the weak points in your supply chain and communicate your expectations clearly with all stakeholders. This includes setting clear SLAs (Service Level Agreements) and ensuring all partners—from trucking companies to terminal operators—are aligned. Strong communication reduces delays and bottlenecks that often lead to fees. If you’re unsure where your communication gaps are, seek expert advice on how to streamline your processes.
One common source of detention charges is inefficiency in how containers are managed, especially when they aren’t returned on time. Get tools that help you monitor your return schedules closely and anticipate delays in trucking or terminal operations. By maximizing container utilization and planning returns carefully, you can cut down on unnecessary detention costs.
Lastly, equip your team with a proactive mindset. Waiting for problems to escalate only results in higher fees. Encourage a culture where issues are addressed before they snowball. This means planning ahead for potential disruptions, aligning with partners regularly, and staying alert to any changes that could impact the movement of your shipments. Proactive management is the best way to prevent demurrage and detention costs from getting out of control.
Simplify ISF compliance for U.S. ocean imports. Learn how Cargoo helps you stay compliant and avoid costly delays.
ICS2 compliance brings new customs compliance challenges for EU imports. Discover key data requirements, roles, and how Cargoo simplifies the process for seamless shipments.
Discover ICS2 compliance essentials for EU imports. Learn how to streamline customs processes and avoid delays with Cargoo’s solutions.